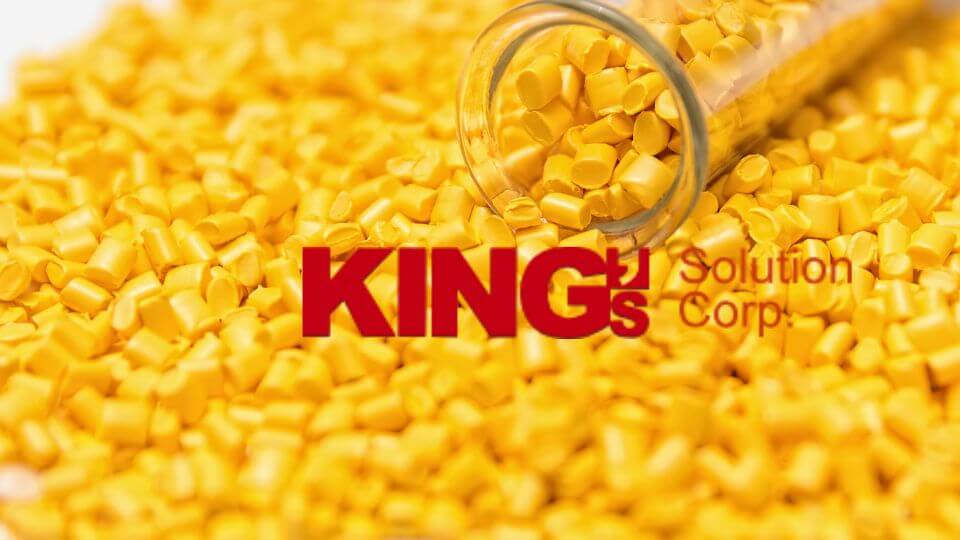
The History of Low Pressure Molding
The development of Low Pressure Molding (LPM) can be traced back to the 1970s, initially gaining popularity in Europe. Early low-pressure materials were already invented, but they were protected by patents held by certain material manufacturers. Over time, as these patents expired, the development of low-pressure materials expanded to other countries, including Germany, Italy, China, and Taiwan. The initial commercial application of LPM technology was in the automotive industry for sealing connectors and wires, while achieving lightweight designs. Approximately a decade ago, Low Pressure Molding began to find applications in various fields, and LPM technology underwent significant breakthroughs, making it suitable for a broader range of applications.
In Asia, while the concept of Low Pressure Molding (LPM) had existed for some time, there was not yet a significant demand for this technology in the market. KING's Solution began its journey into LPM development in 2012-2013. During that period, we actively collaborated with another materials company to embark on the research and development of our proprietary Low Pressure Molding machine. Through this collaboration, we successfully developed a Low Pressure Molding machine in Taiwan and jointly introduced it to several customers.
However, as time passed, we discovered that customers were reluctant to be tied to specific low-pressure materials with our high-quality LPM machines. Therefore, leveraging our position as a green and sustainable machinery manufacturer, we realized that our molding machines were not limited to materials from a particular supplier. They possessed the capability to adapt to various low-pressure materials. We continued to invest in research and development to enhance the efficiency of our Low Pressure Molding machines. Currently, we have reached the sixth generation of smart manufacturing models, which excel in both quality and efficiency.
In Taiwan, despite some other companies entering the same field, they are currently lagging behind KING's Solution by more than 5 to 6 years. It's worth noting that some competitors exited the market after a period because we deeply understand that the bottleneck of Low Pressure Molding is not solely the machinery itself but the provision of complete product solutions to customers. Without a strong foundation in Low Pressure Molding technology and process experience, fulfilling customer product requirements can become exceptionally challenging. Over the years, we have accumulated a wealth of practical product experience, low-pressure material knowledge, low-pressure mold design expertise, innovative process methods, and patent certifications. These assets have enabled us to assist customers in successfully implementing the Low Pressure Molding process. KING's Solution continues to maintain this positioning, making us a leading company in providing comprehensive LPM solutions.
Low-Carbon Advantages of Low Pressure Molding (LPM)
Recently, the surge in Low Pressure Molding processes is driven by the replacement of toxic and cumbersome potting processes. LPM processes eliminate the need for solvents, reducing the use of toxic materials traditionally associated with potting processes. Additionally, LPM processes do not produce harmful fumes during molding. The use of LPM technology results in faster production cycles, lighter components, and environmentally friendly products. This not only improves production efficiency and product yield but also contributes to achieving net-zero carbon sustainability goals. The raw materials used in LPM processes are based on renewable resources, such as vegetable oil, and have been certified by UL for electrical safety while complying with RoHS and REACH standards. Therefore, LPM plays a crucial role in current environmental and sustainability trends, with positive impacts on both our environment and society.
Characteristics of Low-Pressure Materials
Low Pressure Molding technology employs materials such as Polyamide (PA) and polyolefins (hot-melt) among others. These materials are thermoplastic, which means their viscosity decreases when heated, allowing them to be reshaped, and then they harden to maintain the desired shape when cooled. Low Pressure Molding is mainly used for encapsulating and protecting electronic components and is widely employed in manufacturing waterproof sealed connectors. PCB circuit boards, for example, can be affected by moisture, dust, dirt, and vibrations. Continuous breakthroughs and innovations in this molding technology have improved molding efficiency and product quality, making it an integral part of today's manufacturing industry and a driving force behind significant industry transformations.
Polyamide Characteristics
- Impact Resistance: Exhibits resistance to impact and vibrations.
- Ease of Processing: Easy to process and mold.
- Smooth Surface: Products have a smooth external appearance.
- Heat Resistance: Can maintain stability at temperatures up to 140°C.
- Low-Temperature Impact: Maintains some level of strength even at -40°C.
- Excellent Thermal Conductivity: Good thermal conductivity facilitates heat dissipation in electronic products.
- Waterproof Properties: Due to its small molecular size and excellent coverage, it is suitable for waterproof applications in electronic components.
Polyamide, known as Nylon in Taiwan, is a type of engineering plastic, also referred to as hot-melt adhesive. It's important to note that this material is distinct from PVC and is a special engineering plastic based on Polyamide. Polyamide can be enhanced with additives like glass fibers, carbon fibers, and more, to improve strength, toughness, conductivity, and weather resistance.
Sources of Polyamide (PA)
Polyamides primarily originate from synthetic plastics, with their primary components derived from petroleum or natural gas. However, there is another special type of polyamide known as Biopolyamides, which are produced using plant-based oils as raw materials, replacing traditional petroleum-based sources. This makes Biopolyamides an environmentally sustainable material as they rely on renewable plant oils rather than petroleum-based sources.
The extraction of Biopolyamides primarily involves castor oil, a plant-based oil that serves as an alternative to conventional petrochemical materials in polyamide production. Several international companies are actively engaged in the research and development of Biopolyamides:
- Henkel: A notable material supplier based in Germany, Henkel produces LPM materials. These materials exhibit various properties such as UV resistance, thermal stability, excellent molding capabilities, and transparency.
- Cathay: A company based in Shanghai, China, producing "Biopolyamide" where the primary component comes from "Biobased Pentamethylene Diamine," sourced 100% from renewable plant materials.
- Fulgar: This Italian nylon company developed the EVO Biopolyamide fiber, produced entirely from castor oil plants.
- RadiciGroup: A Brazilian nylon manufacturer, its Biopolyamide fiber products Biofeel, Dorix, Radilonru are made from castor oil and agricultural waste, making them 100% renewable.
- Toray: This Japanese fiber manufacturer developed the Biopolyamide fiber ECODEAR PA 6.10, also entirely derived from castor beans.
- Acelon: A Taiwanese company that developed AceEco PA410, a Biopolyamide derived from castor oil, containing 70% castor oil content, and has received Global Recycled Standard (GRS) certification.
Low Pressure Materials: The Superior Choice for Electronics Encapsulation
In conclusion, KING's is a global leader in Low Pressure Molding solutions and is dedicated to research and innovation in the field. We have achieved remarkable success in this domain. We offer comprehensive support to our customers, including hardware and software, local agent services, consultant services, process knowledge, machinery, material recommendations, and mold design. Our goal is to provide reliable, efficient, and eco-friendly Low Pressure Molding technology solutions. As a result, KING's Solution plays a crucial role in driving the development of the next generation of electronic industry packaging. We are committed to providing excellent product realization, technical consultation, and support to our customers.
Low Pressure Molding (LPM) has become the preferred method for protecting modern PCBs and circuits. It maintains a low-pressure environment throughout the entire operation, effectively preventing damage to delicate or fragile circuit boards compared to traditional potting processes.
LPM materials offer superior sealing and adhesion properties, along with excellent resistance to high temperatures and solvents. Additionally, these materials are eco-friendly, halogen-free, non-toxic, corrosion-resistant, and have high flowability with low water absorption. They provide excellent sealing and require low molding pressure.
In summary, Low Pressure Molding materials meet multiple critical requirements, making them an essential choice in the PCB encapsulation process.