Low Pressure Molding (LPM) Process Upgrade: The Low-Carbon Choice for Electric Vehicle Giants
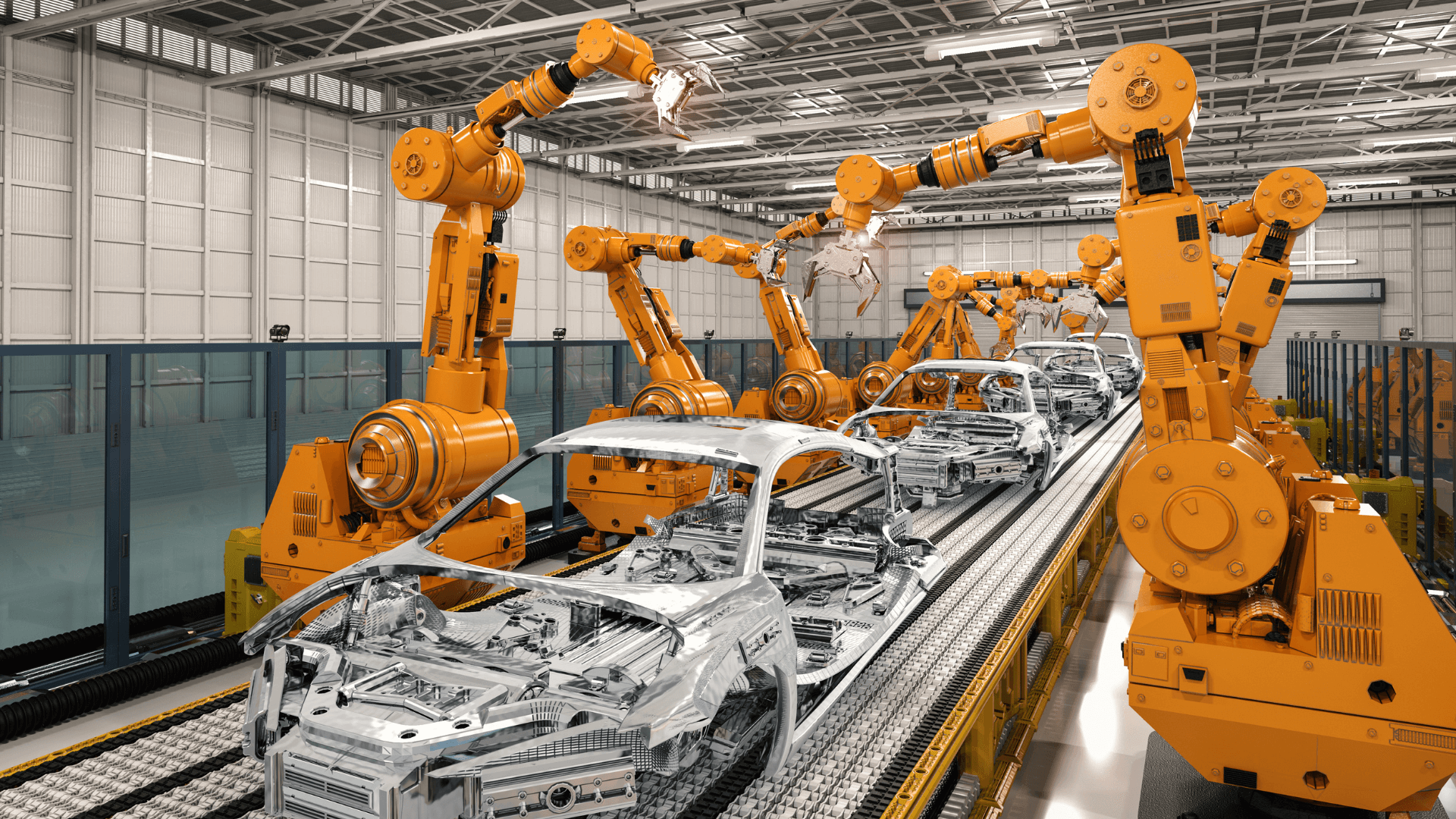
In today's world, ESG (Environmental, Social, and Governance) and carbon emission reduction have become crucial global concerns. Across industries, enormous challenges are being faced, particularly within the manufacturing sector. In this context, Low Pressure Injection Molding (LPM), as an innovative process technology, is gaining increasing importance due to its pivotal role in environmental and carbon considerations.
With electric vehicles representing the future of green energy, manufacturers in this domain need to balance energy efficiency and environmental requirements in their production processes. Low Pressure Injection Molding has emerged as an ideal choice, aiding them in achieving more environmentally friendly production methods.
The Trend of Electric Vehicle Giants Adopting Low Pressure Injection Molding
An increasing number of electric vehicle manufacturers are seeking innovative process technologies to realize greener production processes. Low Pressure Injection Molding, as a solution that meets these demands, has garnered significant attention within the electric vehicle industry. Renowned electric vehicle brands such as Tesla, BMW, Lexus, and others have begun designating suppliers to adopt Low Pressure Injection Molding technology. This trend indicates that Low Pressure Injection Molding has become a significant trend in the electric vehicle industry. The application of this technology will help ensure that production processes align with green sustainable values. For automotive and electronics processing companies alike, choosing Low Pressure Injection Molding technology will be a prudent decision to drive towards sustainable development goals.
The Environmental Advantages of Low Pressure Injection Molding
Low pressure injection molding is an efficient technology for encapsulating electronic components, utilizing a novel low-pressure injection molding technique. This method involves placing electronic components into a mold, heating the material to its melting point (between 180°C-210°C), and rapidly solidifying within seconds to minutes after injection. The swift process allows for immediate processing and testing of electronic components, making Low Pressure Injection Molding a contemporary process technology with significant environmental advantages that are capturing attention across various industries. The following elaborates on the environmental benefits of the Low Pressure Injection Molding process.
Key Characteristics and Benefits of the Low Pressure Injection Molding Process
-
Reduced Manufacturing Costs: Most electronic products consist of components such as circuit boards, chips, and wires. In the past, potting (using epoxy) was employed to safeguard these delicate electronic elements. However, potting processes were intricate and resulted in lower product yield, leading to high production costs. With the efficiency and speed of Low Pressure Injection Molding (LPM), labor costs can be reduced, continuous production achieved, and product yield increased, making it cost-effective for short-term production.
-
Shortened Production Time: The potting process for electronic components used to be time-consuming, involving a wait of 1-3 days for the potting material to solidify before proceeding to the next step. This resulted in a lengthy production cycle with 7-8 production steps. Low Pressure Injection Molding eliminates the need for solidification time, as the cooling time for Low Pressure Injection Molding products takes only seconds to minutes, significantly shortening the manufacturing time.
-
Low-Carbon Eco-Friendly Materials: The materials used in Low Pressure Injection Molding are not only suitable for protecting electronic components but also environmentally safe and non-toxic. These raw materials are sourced from natural components. After production, bio-based polyamide (PA) materials used in Low Pressure Injection Molding are almost 100% recyclable, directly promoting recycling and reuse, which equals zero waste. Furthermore, these bio-based materials can decompose naturally, considerably reducing carbon footprints.
-
Enhanced Product Quality: Low Pressure Injection Molding is favored for electronic product encapsulation due to its lower injection pressure, which avoids adverse effects on sensitive electronic components. The materials used in Low Pressure Injection Molding possess excellent sealing properties, low water absorption, high efficiency, superior corrosion resistance, and strong adhesive properties to electronic components. Therefore, products manufactured using Low Pressure Injection Molding outperform potting in terms of sealing, appearance, and lifespan.
-
High Waterproof Performance: Electronic components in electric vehicles require robust waterproof and dustproof protection to ensure reliability and durability. Low Pressure Injection Molding offers outstanding waterproof capabilities, shielding electronic components from moisture and liquid damage across various environments.
-
Reduced Air Pollution: Comparing Low Pressure Injection Molding to traditional potting processes, the former involves relatively lower temperatures, resulting in reduced greenhouse gas emissions. This method poses a smaller environmental impact compared to traditional potting processes, which could release harmful gases.
Traditional potting processes, such as epoxy potting, come with carbon emission and process limitations.
Below is a comparison between Low Pressure Injection Molding and traditional potting processes in terms of carbon emissions:
|
---|
Low Pressure Injection Molding (LPM) is a novel production technique that offers even more prominent environmental advantages compared to traditional processes. This process can effectively reduce energy consumption and carbon emissions. The higher production efficiency of Low Pressure Injection Molding significantly lowers production costs.
The Importance of Process Upgrade
As electric vehicle giants trend towards adopting Low Pressure Injection Molding, first and second-tier suppliers urgently need to upgrade their equipment and seek professional technical guidance to optimize production processes, achieve carbon neutrality, and respond to ESG (Environmental, Social, and Governance) requirements. The advantages of adopting Low Pressure Injection Molding include:
Enhanced Competitiveness: LPM processes can effectively increase production efficiency while reducing energy consumption and carbon emissions, thereby boosting a company's competitiveness and standing in the market.
Adapting to Carbon Reduction Demands: With escalating environmental requirements, first and second-tier suppliers to automotive manufacturers need to timely adjust their processes by incorporating low-carbon methods, such as Low Pressure Injection Molding, to meet the expectations of both brand manufacturers and consumers.
Waste Reduction: Process upgrades can effectively reduce waste generation and enhance production efficiency, leading to cost-effective reductions. These saved resources can be reinvested in improving product quality and innovation.
KING's Advantages as a Leading Low Pressure Injection Molding Brand
Advanced Technology and Reliable Equipment: KING's is committed to developing and applying advanced Low Pressure Injection Molding solutions, offering customers cutting-edge technology and equipment to facilitate process upgrades.
Professional Knowledge and Experience: As a leading brand in LPM, KING's possesses abundant professional knowledge and successful experience, enabling the provision of effective solutions to customers.
Technical Consultation and Guidance: KING's LPM expertise transfer and technical guidance empowers customers with in-depth understanding of best practices and techniques in Low Pressure Injection Molding, ensuring knowledge and experience are passed on to customers for their benefit.
In conclusion, assisting customers in process upgrades and providing technical guidance is pivotal in realizing and achieving sustainable goals for their products. As a frontrunner in Low Pressure Injection Molding, KING's LPM not only offers advanced machinery and technical guidance, but also significantly impacts the implementation of customers' green and sustainable ideals. This support aids the industry's transformation and customers' green manufacturing endeavors.