PET Preform Injection Molding Machine with 8+8 Cavity Mold
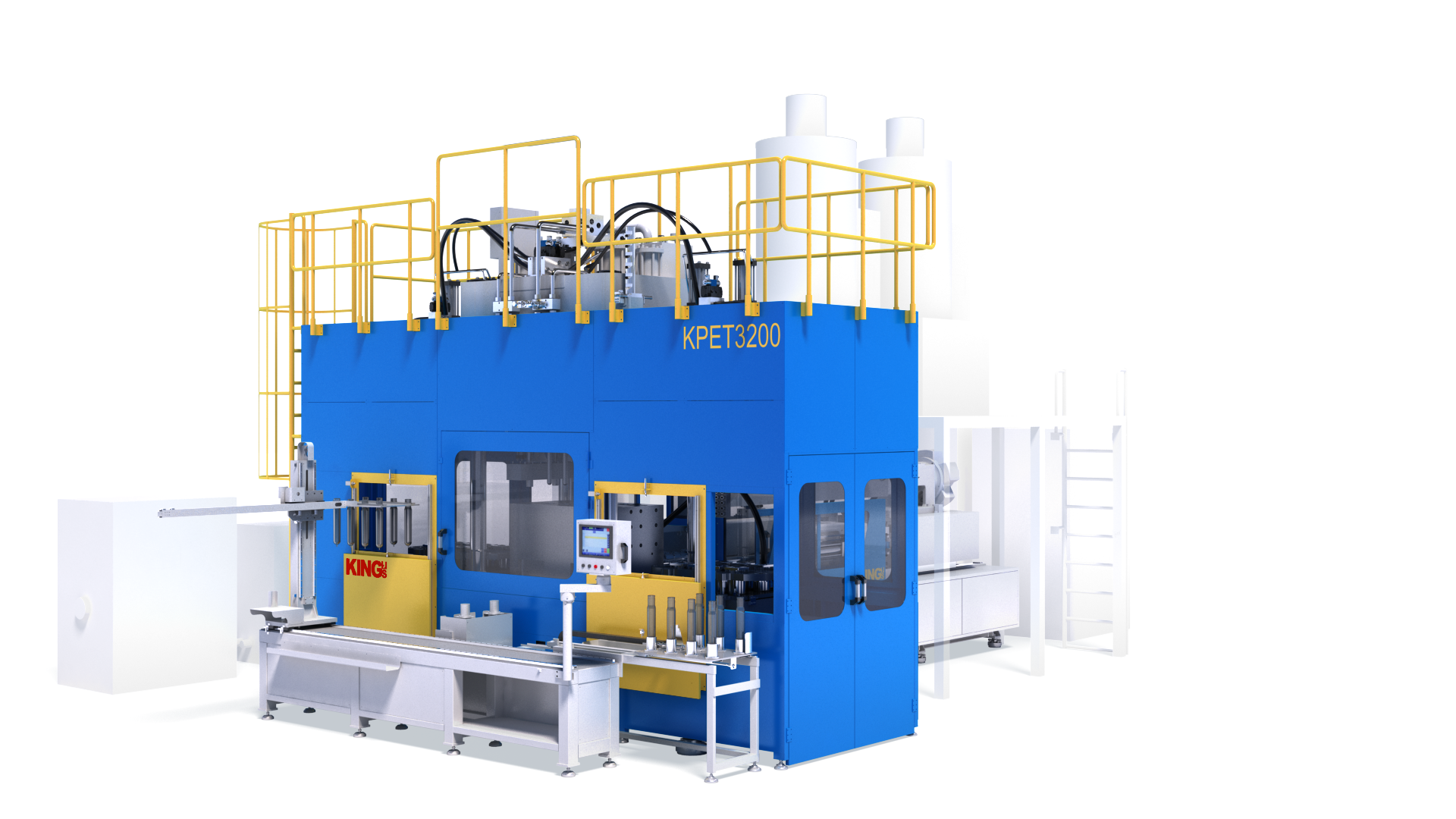
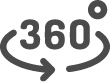
KING’S SOLUTION CORP. acquired 18 years of 5-gallon PET preform making machine practice experience from KING'S MACHINERY ENGINEERING CORP. We provide the full process of Dehumidification Drying raw materials, quantitative additive color mixing machine, rapid and stable injection molding output of bottle preform, mold with 8+8 hot runners, rapid cooling robot mechanism, and the blowing bottle machine itself; Total production cost down with high productivity, and lowest blow bottle defect rate of only 0.5%.
Providing high quality 5-gallon PET Preform skill, we promise to implant production technology into the customer's factory. In response to industry 4.0, KING’S will go across and focus on Big Data capabilities to develop production analytics data open to customers in the near future to form the unmanned factory.
-
Sample Drawing
-
Quotation
-
Confirm PI/PO
-
Design
-
Assembly
-
Machine Testing
-
Mold Trail T1
-
Confirm Sample
-
Mass production
-
Shipment
PET Bottle VS PC Bottle : |
PET | PC |
---|---|---|
Raw Material Cost | Lower | Higher |
Delivery Cost | Lower | Higher |
BPA | Free | Yes |
DEHP | Free | Yes |
Izod Impact Strength | Better | Worst |
A1:PC releases Bisphenol A , it’s been prove to be a cancer risk. BPA is one of the PC material, but some other regions of Europe does not disable PC ( except infant use plastic bottle ), only set limitation of BPA leaching values, i.e. in EU regulations (No 10/2011) , Bisphenol A specific migration limit (SML) for each kilogram is 0.6 (mg/kg).
The cost of PC raw materials is higher than other plastic materials, and the PC machine is extruded whereas the PET machine is injection molding, both PC and PET are in different form of process. The PET bottle has been converted for many years in the plastic industry. Recently, the manufacturer who uses injection machine were not able to use PC materials.
.png?y12ssup82w)
KING’S | Others | |
---|---|---|
Transparency | Transparency | Opaque |
Blow rates | 99% | Unstable |
Ingredient | 100% New material | Mixed material |
Crystal | No Crystal | Crystalized |
Inner Stress | Low | High |
Length | Short(Designed) | Long |
Defect product rate | Low | High |
AA | Low | No control |
For more output request, KPET3200 with Vertical clamping & horizontal injection, adopt patented design:
One extruder screw works with two injection plungers, the PET resin plasticizing, charging never stops by injection/holding process, compared to In-line screw, the drive motor capacity is only 40% but output per hour is the same.
Double shuttle core mold, with Post Mold Cooling system: Double core molds work with one cavity half, save 80% holding/cooling time while molding. Efficient post mold cooling by core mold, preforms keep cooled for one more cycle, ensure the quality and straightness.
Individual setting of injection, with A/ B core molds, can produce two different preform (inner dia, and neck design) at the same time.
Vertical Clamping and upward mold flow the melt material injected from the bottom upward, with balance mold flow and even air vent, preform stress low, not welding line/ bubble.
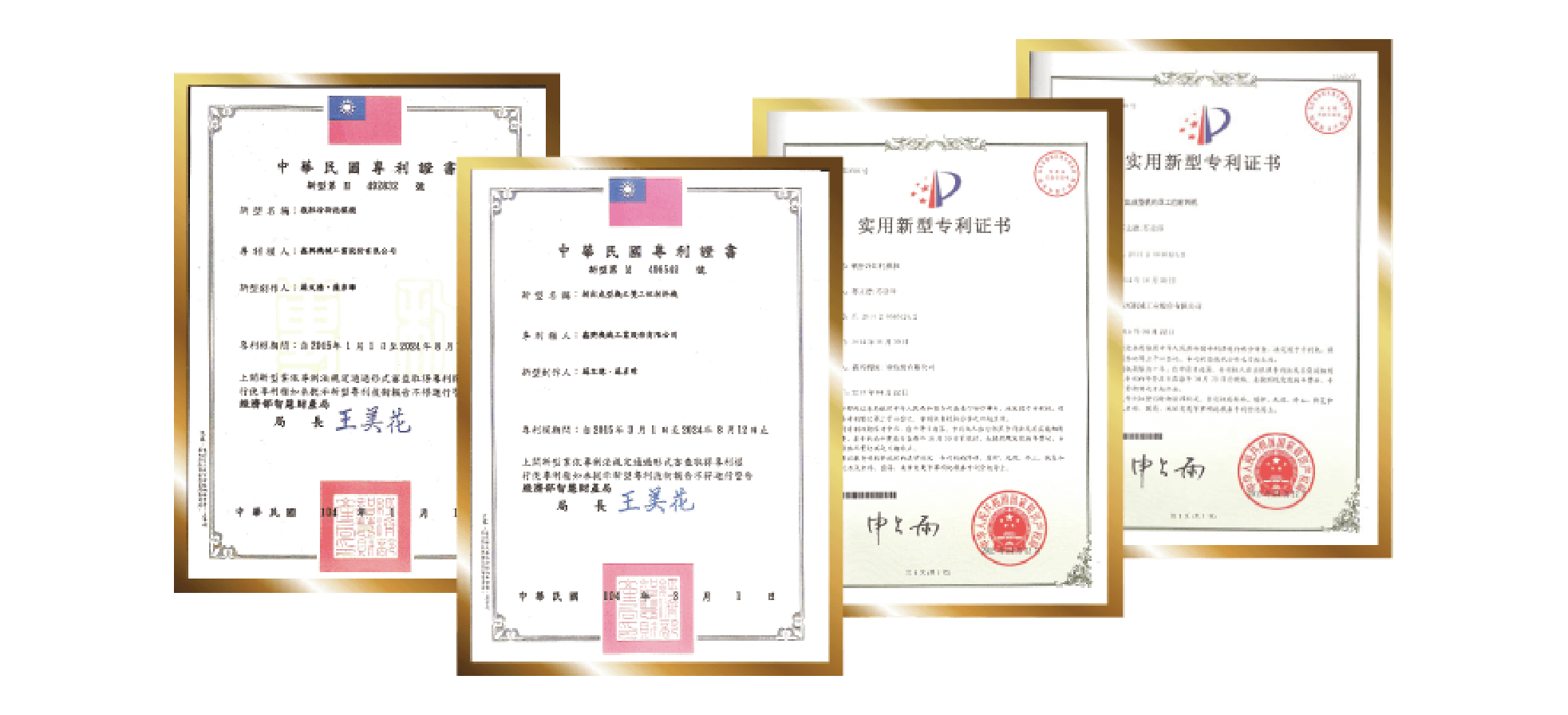
![]() |
![]() |
![]() |
|
---|---|---|---|
Model | Others | KPET-1600 | KPET-3200 |
KPI | 1st single cavity | 2nd 4 cavity mold | 3rd 8+8 cavity mold |
Energy saving (per Preform) |
Motor 1.13 / kwh Heater 0.17 / kwh |
Motor 0.46 / kwh Heater 0.15 / kwh |
Motor 0.065 / kwh Heater 0.058 / kwh |
Cycle time | 100 sec / 1 pc | 130 sec / 4 pcs | 90 sec / 8 pcs |
Production | Single cavity, 720 pcs / day | 4 cavity, 2400 pcs / day | 8+8 cavity, 7200 pcs / day |
Power consumption (per kWh) | 1.3 kWh / pcs | 0.61 kWh / pcs | 0.145 kWh / pcs |
Saving Energy for |
![]() |
W-LINE Injection System
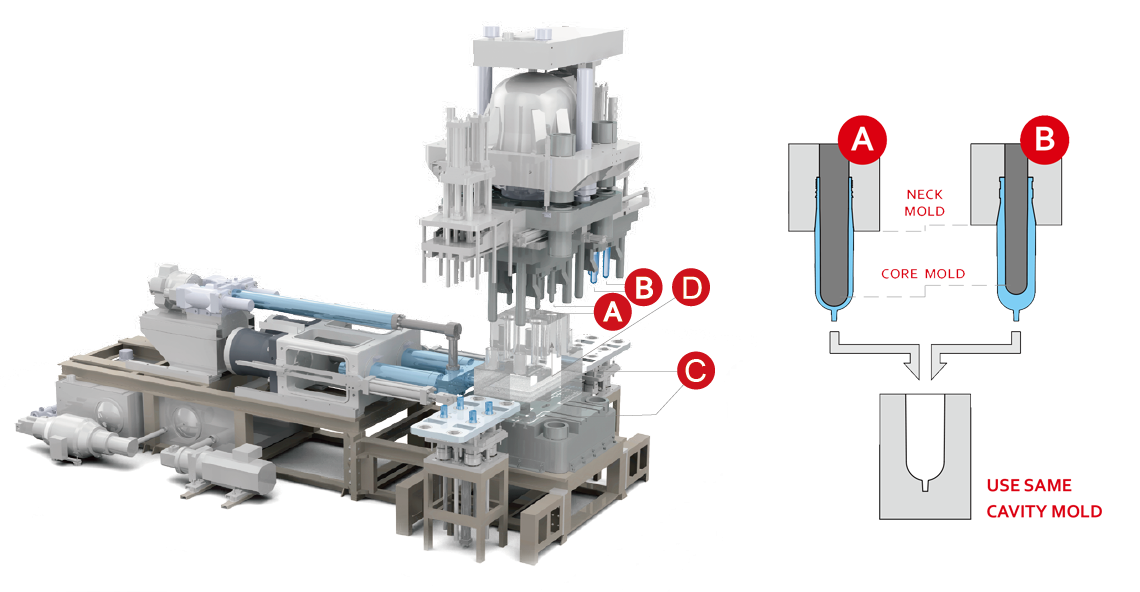
Individual setting of injection (EX:A、B)
- Individual setting of injection, with A/ B core molds, can produce two different preform ( inner dia, and neck design) at the same time.
Vertical Clamping and upward mold flow (EK:C)
- The melt material is injected from the bottom upward,with balanced mold flow and even air vents, preform stress is low, no-welding line/bubble.
Double shuttle&core mold , with Post Mold Cooling system: (Ex:D)
- Double core molds work with one cavity half, saves 80% of holding/cooling time while molding. Efficient post mold cooling by core mold, preforms keep cooled for one more cycle, ensure the quality and straightness.
W-LINE Injection System

one extruder screw work with two injection plungers, the PET resin plasticizing , charging never stop by injection/holding process, compare to In-line screw (ex:A、B)
- One extruder screw work with two injection plungers, the PET resin plasticizing,
- charging never stop by injection/holding process,
- compare to In-line screw, save 80% energy in charging.